Background
A customer had a large installation with a pellet boiler, solar hot water panels, heat storage, and propane backup that provided heat and hot water for several buildings. The system was a few years old, and they felt that it wasn’t performing as well as it should. For a variety of reasons, the original system designers and installers were no longer involved or available.
Symptoms
The owners observed that the system did not produce consistently hot water, requiring the propane backup to be used if rapid heating was needed. Total heat production from the solar panels was much less than expected, and the pellet boiler ran more often than it should.
Step 1: Document and Monitor
Vermont Energy Control Systems documented the as-built plumbing and installed a Vesta system to monitor temperatures at key points in the system. The Vesta was configured for remote access. We monitored the following temperatures:
- Storage Tank 1 top and bottom
- Storage Tank 2 top and bottom
- Pellet boiler supply and return
- Solar panel array supply and return (panel side of heat exchanger)
- Solar panel heat exchanger supply and return (tank side)
- Supply and return from heat loads
Review of temperature data confirmed that the system was not performing well, and helped pinpoint several problems.
Problem 1: No Stratification
The temperature at all points in storage was virtually identical at any point in time. Storage was heating and cooling as a unit, cycling between about 150 and 180. That caused three performance issues:
- The water temperature available to the heat loads was too cool most of the time. The hottest temperature available in storage was almost always less than 180, and less than 170 more than half the time.
- There was no cool water to send to the solar panels. The coolest water available averaged about 165.
- The pellet boiler also didn’t have cool water to work with. That’s not a big problem most of the time, but as inlet temperatures exceed 170, the boiler can’t flow enough water to absorb its full output without exceeding its maximum allowable outlet temperature.
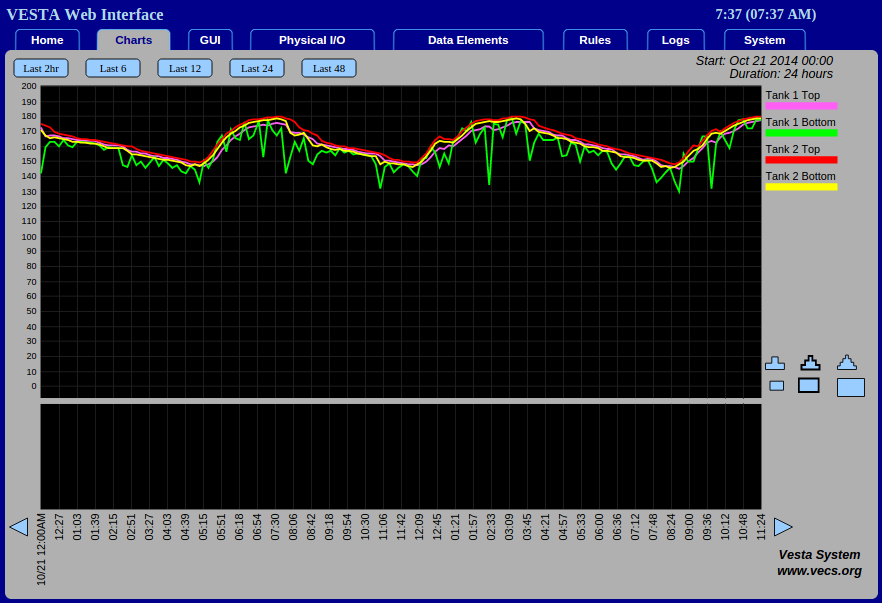
Figure 1: No Stratification in Storage
Root Cause 1: Plumbing Errors
An investigation of the plumbing revealed two serious errors. A diverter valve was installed in the boiler return line instead of the boiler supply line, and there was an unintended return path that allowed a ‘short circuit’ from the boiler supply to return.
Root Cause 2: Design Issues
The original design did not support the idea of thermal stratification, and in fact had a pump that effectively destratified both tanks under certain conditions.
Root Cause 3: Control Issues
The controls for the system consisted of a very large and elaborate industrial control cabinet with a sophisticated solar system controller, a PLC, a couple of standalone third-party controllers, and an enormous amount of relay logic. The documentation was extensive, but not complete or accurate. There was no overall ‘theory of operation’, and no documentation on the solar controller configuration or PLC code.
The control system turned things on and off at times and conditions that didn’t always make sense.